Complex 3DFilament Winding for CFRP and Hybrid Materials CIKONI Innovate. Develop. Realize

Filament Winding
The benefits of carbon fiber filament winding Filament winding is well suited for automation, providing end products that are high in strength and low in weight. The controlled variables for winding are fiber type, resin content, winding angle, tow or bandwidth, and thickness of the fiber bundle.
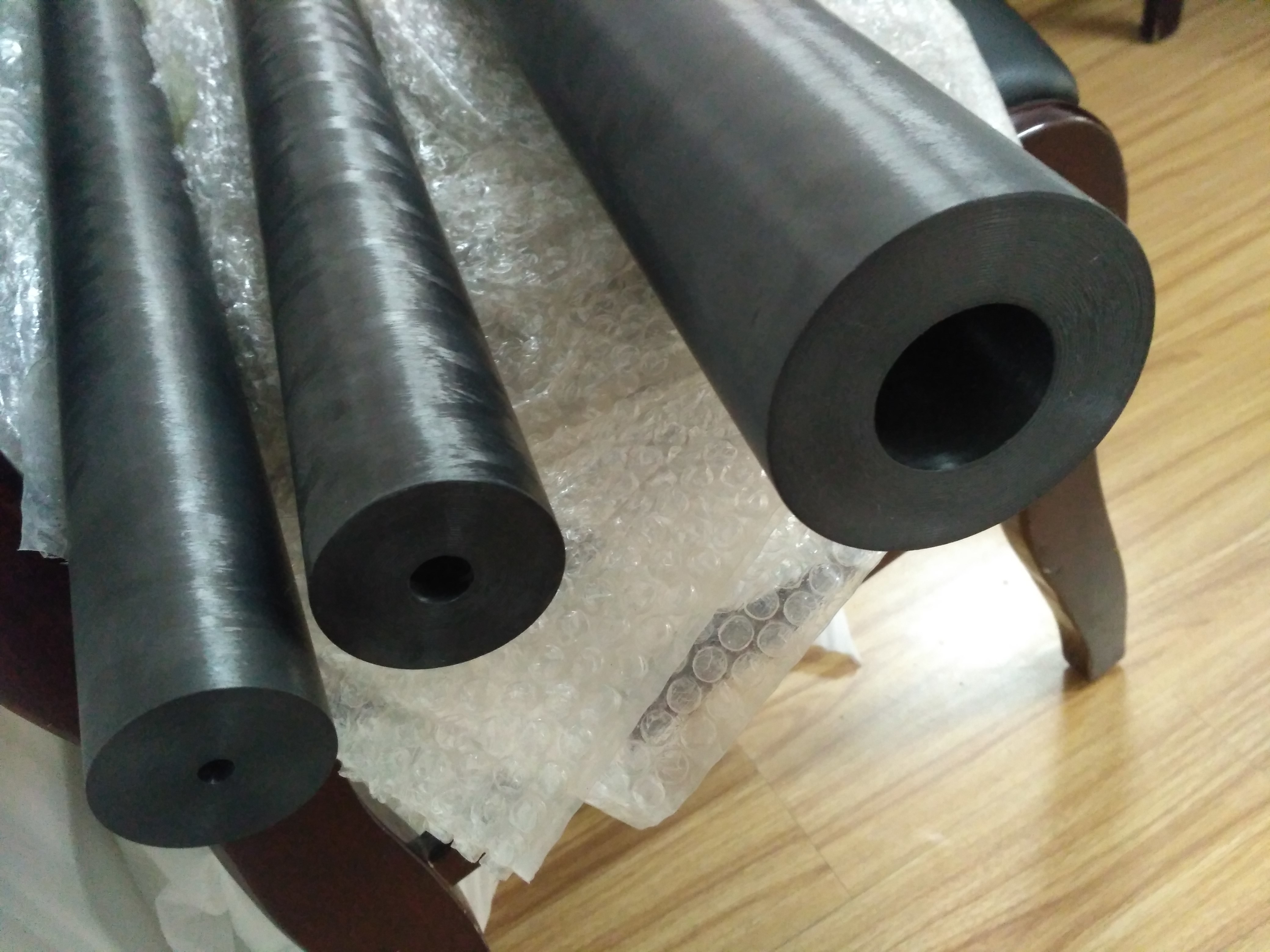
filament winding carbon fiber tube pipe with thicker thickness Toray T700
Filament winding is a composite manufacturing process which involves wrapping a fibre tow over a mandrel. Here Carbon fiber is being wound over the mandrel to create a cylindrical part..

Carbon Fiber Filament Winding Machine BEST 3D PRINTING
Filament winding is an automated, high quality production process utilizing an impregnated roving (e.g. carbon fiber or glass fiber) which is laid on a rotating core and thereby forming a composite vessel, pipe or any rotation-symmetric fiber composite part.

Complex 3DFilament Winding for CFRP and Hybrid Materials CIKONI Innovate. Develop. Realize
Composite Envisions LLC. 8450 Development Court. Wausau, WI 54401. 715-842-0101. Filament winding is a manufacturing process using continuous strands of tow from various materials such as carbon fiber Kevlar or fiberglass to yield hollow tubular parts. This process is used in vast number of applications for making tubular parts such as rocket.

Filament Winding Boosts Production Efficiency for Selip Magnum Venus Products
Filament winding is one of the main composite manufacturing processes, in which composite parts are produced by laying fibers in prescribed patterns [ 1 ]. It is one of the most energy-efficient processes in composite manufacturing [ 2 ]. It is a well-established, fast and cost-effective process to manufacture fiber-reinforced composite parts.
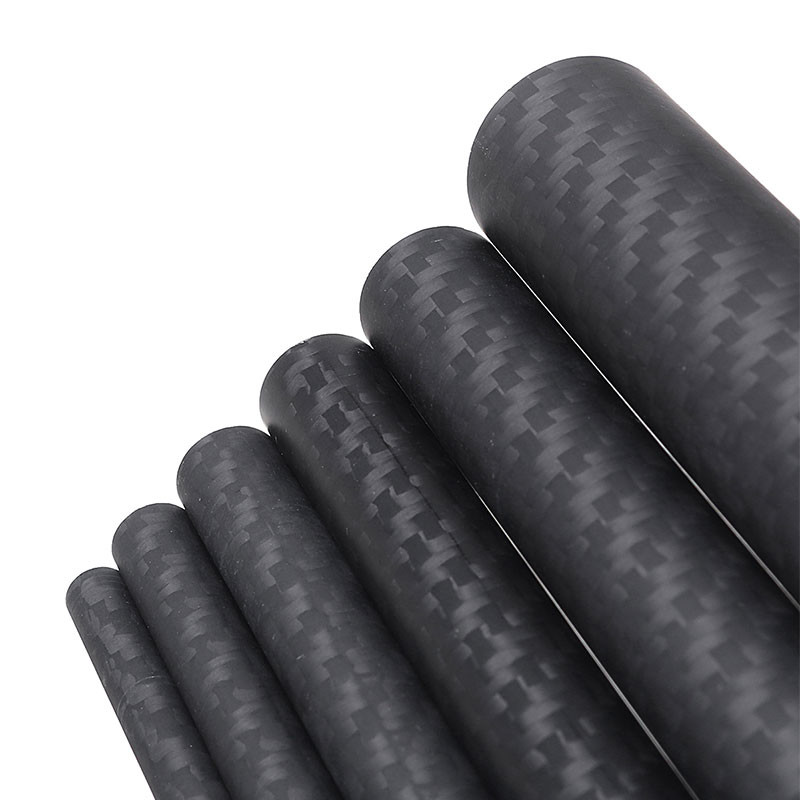
High Modulus Filament Winding Carbon Fiber Tube Corrosion Resistance
Filament winding has emerged as the main process for carbon fiber reinforced plastic (CFRP) fabrication, and tension control plays a key role in enhancing the quality of the winding products. With the continuous improvement of product quality and efficiency, the precision of the tension control system is constantly improving. In this paper, a novel tension control method is proposed, which can.

Filament Winding Carbon Fiber YouTube
The main idea is to place a TFP patch in between two filament wound layers aiming at maximizing the load transfer between the parts. To assess its feasibility, physical properties, such as density, fiber volume fraction and void content, and also the hybrid process kinematics and error propagation are evaluated.

Carbon Fiber Filament Winding Machine YouTube
Filament Winding Ginger Gardiner Senior Technical Editor, CompositesWorld "FibreTEC 3D" This robotic gripper for automotive assembly weighs 50% of a standard aluminum version. It is made with the FibreTEC3D process, which winds carbon fiber tow impregnated with epoxy around aluminum pins with zero waste. Source | Daimler AG

Filament Winding Carbon Fiber Tube 20190822 2 YouTube
Best recommended Products for Filament Winding SikaBiresin® CR84 (formerly Biresin® CR84) Composite resin system for filament winding process with T g up to 94 °C SikaBiresin® CR141 (formerly Biresin® CR141) Composite resin system for advanced processes with T g up to 139 °C SikaBiresin® CR201 (formerly Biresin® CR 201) Get in touch Contact us

INOWIND Filament Winding System Carbon Fiber Shaft Winding YouTube
Filament winding is a technique primarily used to manufacture hollow, circular, or prismatic parts such as pipes and tanks. It is performed by winding continuous fiber tows onto a rotating mandrel using a specialized winding machine. Filament wound parts are commonly used in the aerospace, energy, and consumer product industries.

Carbon fiber filament winding wrap 3 YouTube
The filament winding process, especially in its early stages, was quite manual, involving steps like manually loading mandrels, mixing resin, tying fibers to the mandrel, changing fiber types, cutting rovings post-winding, and unloading the wet-wound mandrels into the oven.
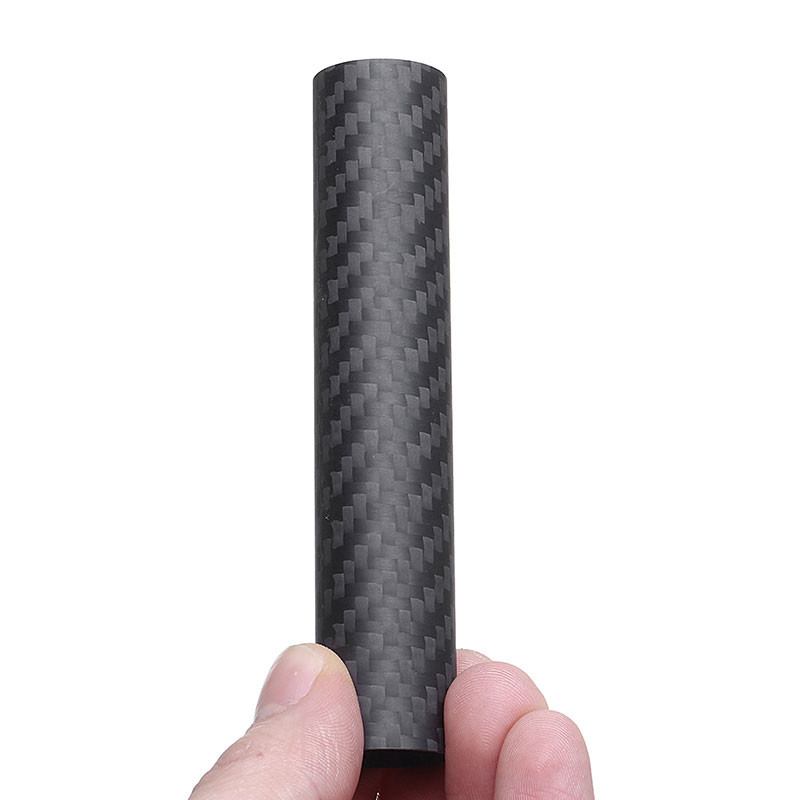
3K Filament Winding Round Carbon Fiber Pipe High Modulus
open access Abstract During the manufacturing of composite pressure vessels, the fiber tension of the filament winding process has an important influence on the mechanical properties as well as on the gravimetric efficiency of the structure and is therefore investigated within this paper.
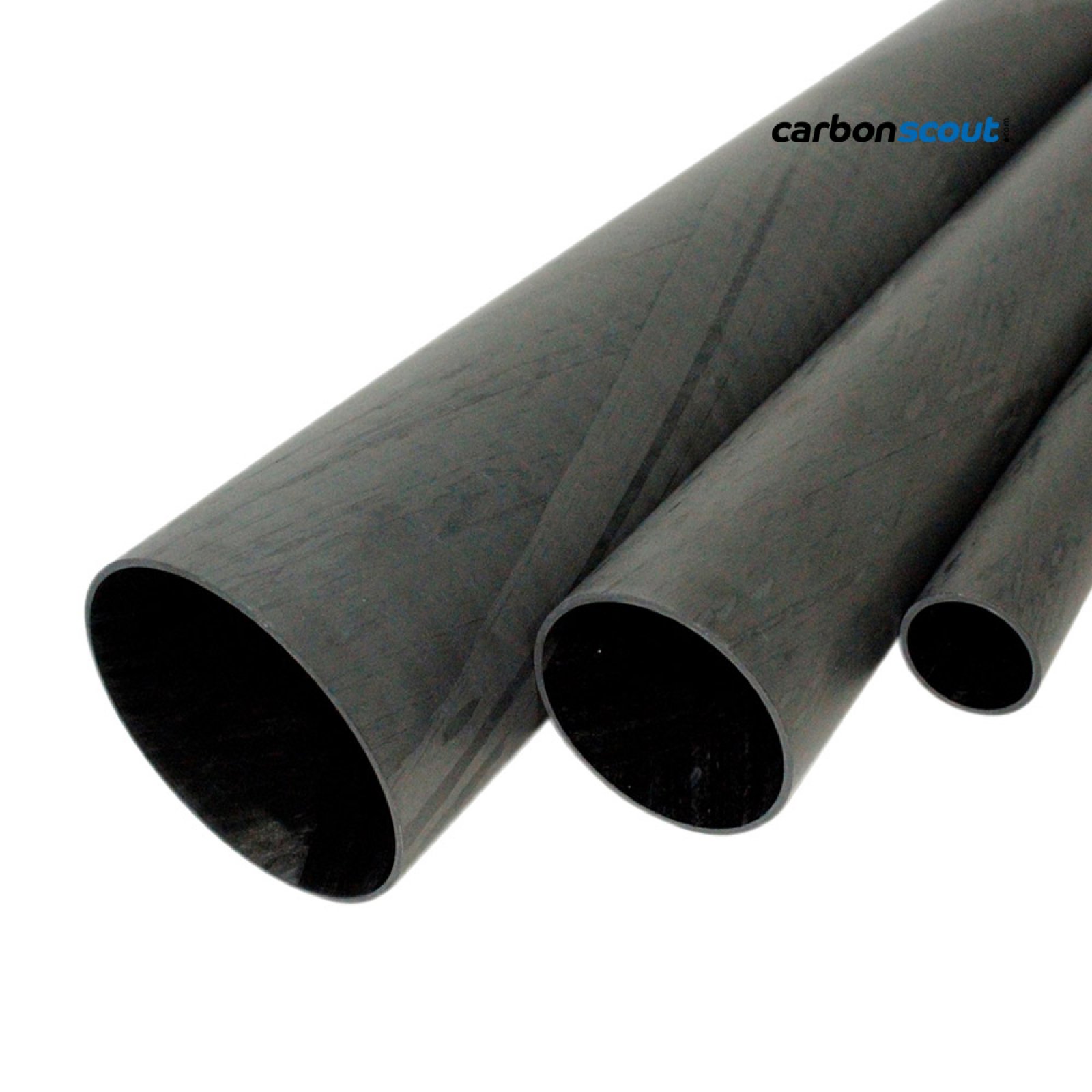
CFRP carbon filament winding tubes 104x100
The filament winding process involves two primary components. A stationary steel mandrel rotates, while a carriage arm travels horizontally up and down the length of the mandrel. The traveling arm includes a winding eye, which groups the rovings—typically of carbon, fiberglass, or a mixture of the two—and dispenses them to the mandrel.

large diameter filament winding sanded carbon fiber tube with high strength for sale filament
Composition: 0.3 mm wall thickness, high temp cyanate ester resin, sleeved design Benefits: Extreme light weight design, high temperature stability CFRP projects for space missions JUICE RIME CFRP folding antenna for the Radar for Icy Moons Exploration (RIME) of the JUpiter ICy Moons Explorer mission (JUICE) Learn more GRACE-FO

Complex 3DFilament Winding for CFRP and Hybrid Materials CIKONI Innovate. Develop. Realize
Filament winding machines in which the motions for positioning, wrapping, and winding fibres are coordinated and programmed in three or more axes, specially designed to fabricate composite structures or laminates from fibrous and filamentary materials and capable of winding cylindrical rotors. Radioactivity in the Environment, 2000 About this page
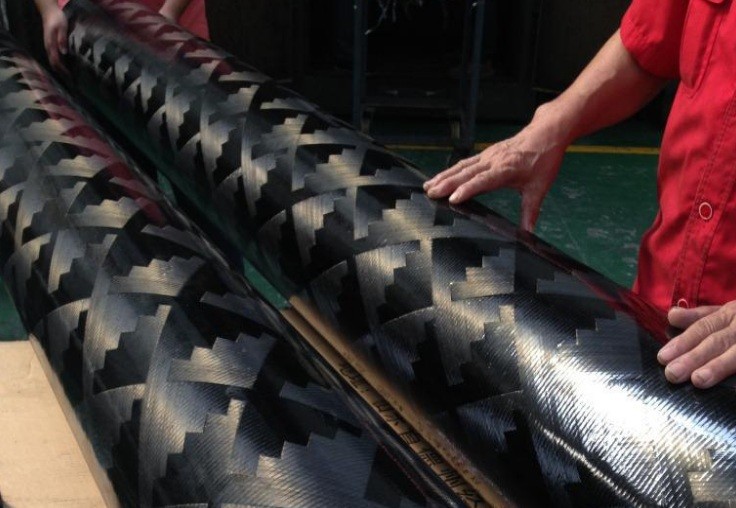
large diameter filament winding sanded carbon fiber tube with high strength
Filament winding is a specialized technique used in composite manufacturing, involving the precise and automated winding of continuous fibers onto a rotating mandrel or mold. This method allows for the creation of strong and seamless structures, optimizing the alignment and orientation of the fibers to meet specific design requirements.